General data
CYPE 3D analyses any type of structure with bars (linear elements) made of concrete, steel, composite concrete and steel, aluminium, timber, or any other material, and includes the design of connections (welded and bolted connections of rolled and welded steel I sections and hollow structural sections) and their foundations with baseplates, footings, pile caps, strap and tie beams. Timber, steel or aluminium bars and reinforced concrete columns and beams can be designed by the program. Composite concrete and steel columns can be checked by the program.
Operating as an independent program, CYPE 3D also allows the discretisation of structures using shells (flat two-dimensional elements of constant thickness whose perimeter is defined by a polygon) to analyse their forces and stresses.
It analyses, designs and checks the fire resistance of timber sections; it checks the fire resistance of steel sections and designs the protective coating for steel sections. It carries out the seismic analysis of the structure. For wind and seismic loads, it considers second-order (P-delta) effects.
CYPE 3D also works as an independent program, as well as within CYPECAD as an integrated 3D structure.
Work environment
The CYPE 3D work environment is similar to other CYPE modelling tools and features a system of dockable windows that can be customised to adapt the workspace to the project's needs.
At the bottom left of the screen, there are two separate tabs: "Structure" and "Foundation".
On the left-hand side are the main tools for defining project tags and managing the visibility of categories, as well as other display options.
The modelling area is located on the right-hand side of the start screen and is where all the elements of the project are entered, edited and displayed. Users can choose how the elements are drawn: schematically or in 3D. This selection can be made independently for each tag.
The main toolbar contains different features depending on the "Structure" or "Foundation" tab.
Limit states, loadcases, combinations and loads
Limit states
Different limit states can be configured for each material.
The program also allows users to view and print a report with the project situations, with and without seismic loads, showing the γ partial safety coefficients (load amplification factors) and the ψ combination coefficients for each type of load (nature).
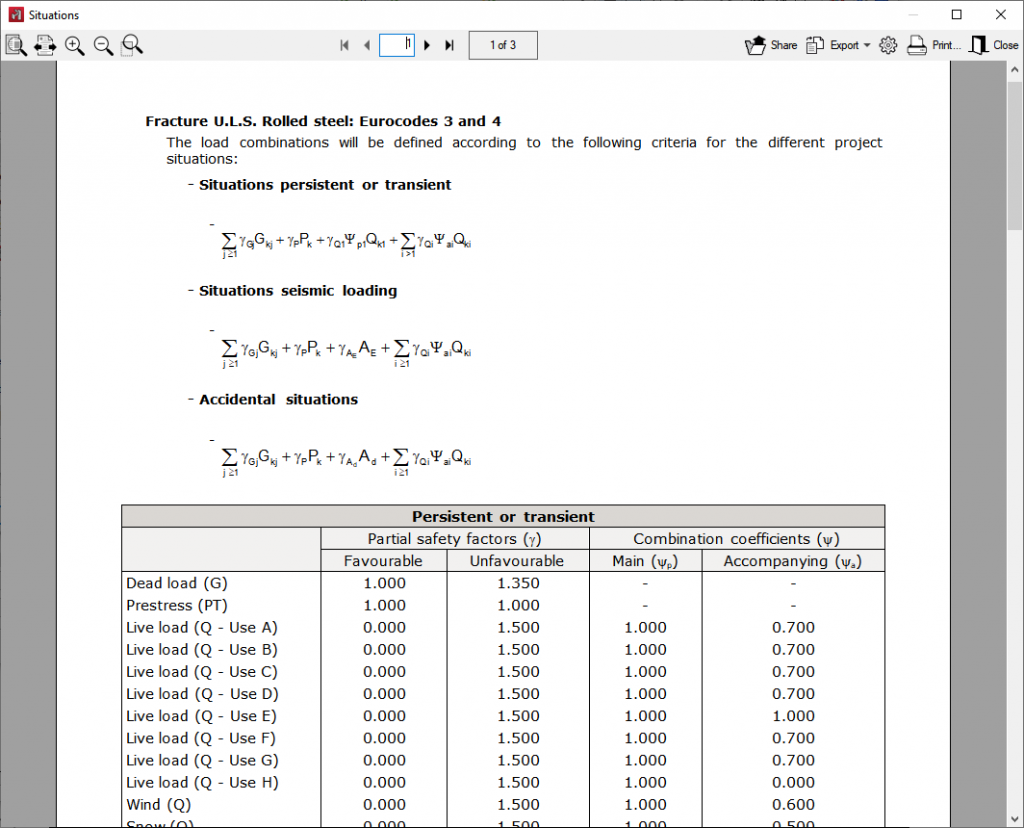
Loadcases and loadcase combinations
CYPE 3D automatically generates the self-weight of the entered bars that will form a self-weight loadcase. An indefinite number of additional loadcases of the same or different nature (self-weight, live load, wind, seismic or snow) can be added.
Users can define any number of simple loadcases and decide whether to combine them in a compatible, incompatible or simultaneous way. The program will automatically generate the combination of these loadcases according to the indicated conditions.
For example, the program automatically generates the loadcase combination corresponding to a load situation consisting of a generic overload and the performance of a load trolley with different positions. The trolley positions are incompatible with each other, but each of them is compatible with the generic overload and with the other loadcases of different nature.
The generated loadcase combination among the loadcases of the same nature can be viewed. This way, users can check whether or not the indicated conditions are correct.
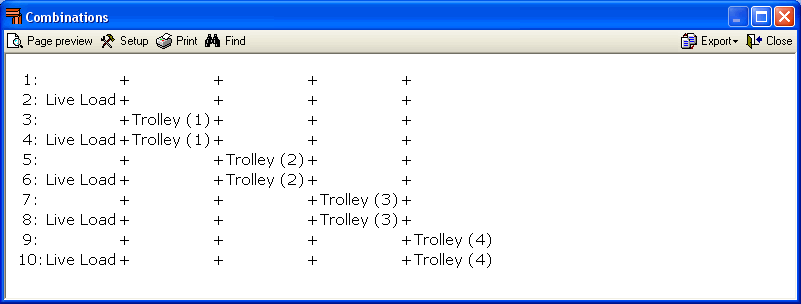
Multiple load types
The program supports multiple types of loads such as point load, uniform load, strip load, left and right triangular load, trapezoidal load, surface with height variation, increase in uniform and variable temperature, applied moment, etc. The loads can be introduced on nodes and bars.
Surface loads are introduced on panels that have been geometrically defined by the user by means of a closed polygon. These loads can be applied on the entire surface of the panel or on polygonal surfaces contained in the panel. Users also indicate the direction of the unidirectional distribution of the loads introduced on the panel, which must be parallel to one of the sides of the panel.
The distribution of all the loads applied on the panel is isostatic and is carried out on the bars contained in the panel that are not parallel to the distribution direction. For loads defined on the surface of the panel, the distribution will only affect those bars that are closest to the defined surface.
In the 3D structures integrated into CYPECAD, surface loads can also be defined in the same way as in CYPE 3D. More detailed information can be found in the following videos:
It is possible to define prescribed displacements in the fixities and supports and prescribed rotations in the fixities. These displacements and rotations will cause forces in the bars so when they are defined, their effects must be assigned to a loadcase.
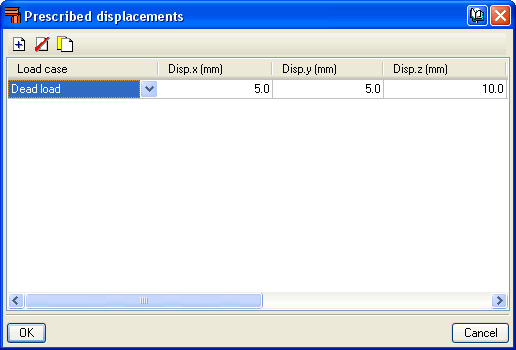
Node types
The node type selection is very complete. Both internal and external fixities can be defined. External fixities allow nodes to be defined as pinned, fixed or partially fixed, elastic supports (springs), supports with free displacement according to a plane or straight line to be defined, etc.
Ties can be defined between nodes. These node ties are used to indicate that two or more nodes have equal displacements in all the loadcases. This matching of displacements can be established in one, two or three directions in accordance with the global X, Y and Z axes. The number corresponding to each group or set of nodes whose displacements are linked is shown on screen.
It should be noted that for two or more nodes to have equal displacements between them, there must be some element or constructive arrangement in the structure that effectively implements the loadcase of equal displacements.
Ties cannot be assigned to nodes that are part of the edges of braced frames when the tied displacement is projected onto the plane of the braced frame.
Bar structure types in CYPE 3D
CYPE 3D allows users to enter bars made of concrete, steel, composite concrete and steel, aluminium, timber or any other material.
The program designs the section reachingthe optimum size for steel, aluminium, timber or concrete bars (if their structural type has been defined as a column or beam).
Composite concrete and steel bars can be defined if they have been entered as column-type structural elements and, although they are not designed automatically, they are checked by the program with the properties indicated by the user.
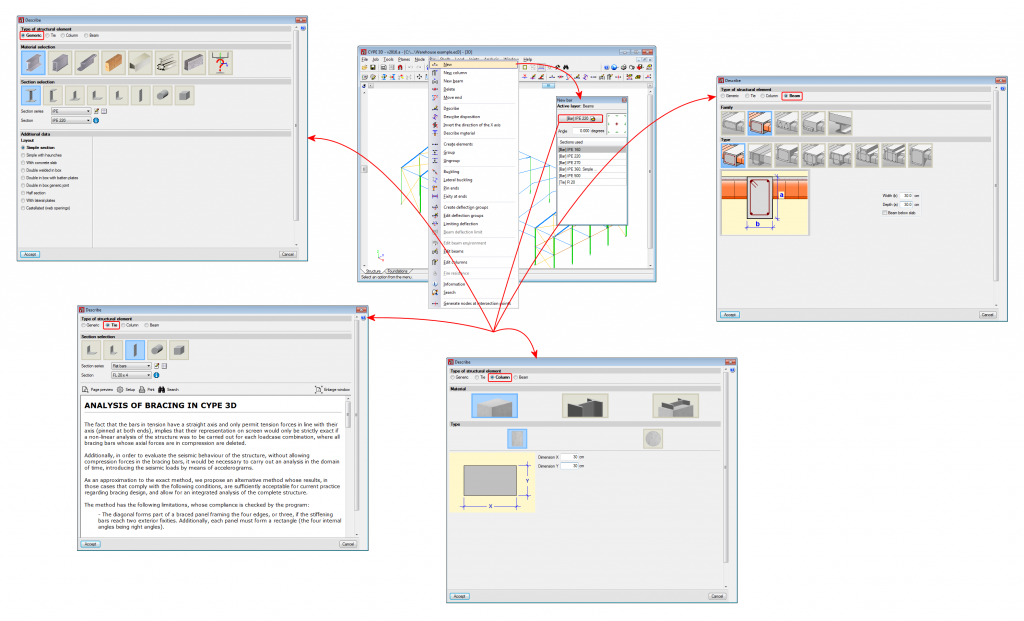
Entering beam and column concepts in CYPE 3D implies characterising the bars in the model as belonging to a structural element type. As of version 2016.a in CYPE 3D, bars are assigned to one of the following four types of structural elements:
"Generic" type structural elements
Elements defined this way do not have a specific structural role in the program. The materials they can be assigned to are steel (rolled, welded or cold-formed), aluminium, timber, concrete or any other user-defined material (modulus of elasticity, Poisson’s ratio, coefficient of thermal expansion and unit weight).
The program designs the bars automatically if the assigned material is rolled, welded or cold-formed steel, aluminium or timber.
If the assigned material is reinforced concrete or a user-defined generic material, the program analyses the forces to which these bars are exposed and displays the results for each simple loadcase, by combinations and by envelopes, but their sections are neither checked nor designed. To check and design reinforced concrete bars in CYPE 3D, they must be defined as "Column" type or "Beam" type structural elements.
More information on these structural elements can be found on the Bars defined as "Generic" type structural elements webpage.
"Tie" type structural elements
The element is part of a braced frame and only works in tension. Transverse sections that can be assigned include flat bars, angles, and solid round or square bars.
More information on these structural elements can be found on the Bars defined as "Tie" type structural elements webpage.
"Column" type structural elements
The element is a column and must be vertical. It accepts the following sections:
- Rectangular and circular reinforced concrete sections
More information on this module used by CYPE 3D and CYPECAD, which allows both programs to design these structural elements, can be found on the Concrete columns webpage. - Steel sections
These can be made of rolled steel, cold-formed steel or welded steel. - Composite steel and concrete sections
More information on this module used by CYPE 3D and CYPECAD, which allows both programs to design these structural elements, can be found on the Composite steel and concrete columns webpage.
More information on these structural elements can be found on the Bars defined as "Column" type structural elements webpage.
"Beam" type structural elements
The element is a beam. It cannot be vertical and must not be rotated about its longitudinal axis. It accepts the following sections:
- Rectangular section, L-beam, T-beam, etc., lattice or prestressed concrete beams
More information on this module used by CYPE 3D and CYPECAD, which allows both programs to design these structural elements, can be found on the Concrete beams webpage. - Steel sections
These can be made of rolled steel, cold-formed steel or welded steel.
When an element is defined as a beam, the beam is composed of a single element. Nonetheless, the program allows users to define continuous beams composed of several beams. - Timber
These can be made of rectangular sections of sawn or laminated timber. More information on this module used by CYPE 3D and CYPECAD, which allows both programs to design these structural elements, can be found on the Timber sections webpage.
More information on these structural elements can be found on the Bars defined as "Beam" type structural elements webpage.
Other properties of bars
Buckling and lateral buckling
CYPE 3D allows users to introduce the ß buckling coefficients or buckling length, the moment coefficient and the C1 coefficient of the lateral buckling critical moment formulation (if defined by the selected code) of each bar. Each code normally provides values for these coefficients associated with different bending moment distributions between bracing points.
The program also automatically calculates the buckling length of the bars according to an approximate method, based on commonly accepted formulas, that requires users to classify the structure as a sway frame or a non-sway frame. Users can also activate the lateral buckling check for any bar.
Deflection limitation
The program allows users to limit the deflection of the bars so that the design of the sections takes into account the imposed restriction (as well as the stress, slenderness, buckling, etc). Users may limit the maximum and relative deflection, both for their absolute and relative values to the length between ends and inflection points of the deformed shape. The deflection may be defined as secant or tangent at one of its ends. An element composed of various aligned bars can also be defined so that the program checks its deflection as if it were a single bar. The dialogue boxes limiting the deflection of the bars have help captions available that perfectly define the different types of deflection that users may limit and the length that serves as a reference for the relative deflection.
Adjustments, displacements and rotations
When introducing bars, it is possible to carry out adjustments, displacements and rotations with respect to their introduction axis. The eccentricity produced by these adjustments and displacements is taken into account in the analysis, so the program allows users to consider the true relative position between bars.
Fixity coefficients and rotational stiffnesses
The program allows XY and XZ fixity coefficients or rotational stiffnesses to be assigned to the ends of elements (bars or groups of aligned bars forming an element) in these planes. Defining the rotational stiffnesses allows connections that require the consideration of their stiffnesses to rotate, such as bolted connections, to be modelled.
For each designed bolted connection, the program also analyses (for all the acting force combinations) the rotational stiffness of each element fixed to the connection and selects a rotational stiffness value for each element end, which will be that proposed by the user for re-analysing the structure.
Once the analysis has concluded, the program provides a warning if the rotational stiffness entered by the user for the elements fixed to the bolted connections differs by more than 20% from that proposed by the program or if it has not been defined.
CYPE 3D allows users to automatically assign the rotational stiffnesses proposed by the program as well as revise any they wish to check in order to decide which rotational stiffnesses are to be adopted.
More information on the considerations CYPE 3D carries out on rotational stiffnesses can be found in the "Rotational stiffnesses at element ends" section on the Bolted joints page.
Shells in CYPE 3D
CYPE 3D allows users to define shell elements. Shells are flat two-dimensional elements with constant thickness and without openings, whose perimeter is defined by a polygon.
For analysis purposes, shells are introduced in the global stiffness matrix of the structure using a three-dimensional finite element model composed of six-node (quadratic) triangular flat shells. The type of element used is based on the overlap of two locally decoupled elements: one provides the axial stiffness (membrane forces) and the other the bending stiffness (panel forces).
The following properties can be defined for each shell:
- Thickness and subgrade modulus
E in the local Z axis direction. - Material
Concrete, rolled steel, cold-formed steel, aluminium and generic material (specifying the modulus of elasticity and Poisson’s ratio). - Position
With respect to the introduction plane. - Discretisation
The density of the mesh can be controlled by defining the maximum size of the triangle in the local x and y axes. - Direction of the axes
- Internal fixity
Internal fixity between the edges and other elements of the structure. - External fixity
The external fixity of the edges can also be defined, but in this case, the fixity is applied to all the shells sharing that edge. The possible external fixity configurations are the same as those available for nodes in CYPE 3D. - Integration strips
Integration strips in shells define lines on which, for a given strip width, the forces corresponding to the shell are integrated to obtain the bar forces.
In order to be able to use shells in CYPE 3D, the user license must have the permits required for the CYPE 3D program.
More information on these new elements that can be introduced and analysed in CYPE 3D (interaction with other elements in the structure, data introduction, load definition, force consultation, etc.) is available on the Flat shells webpage.
Some graphic examples of structures created with shells in CYPE 3D are shown below:
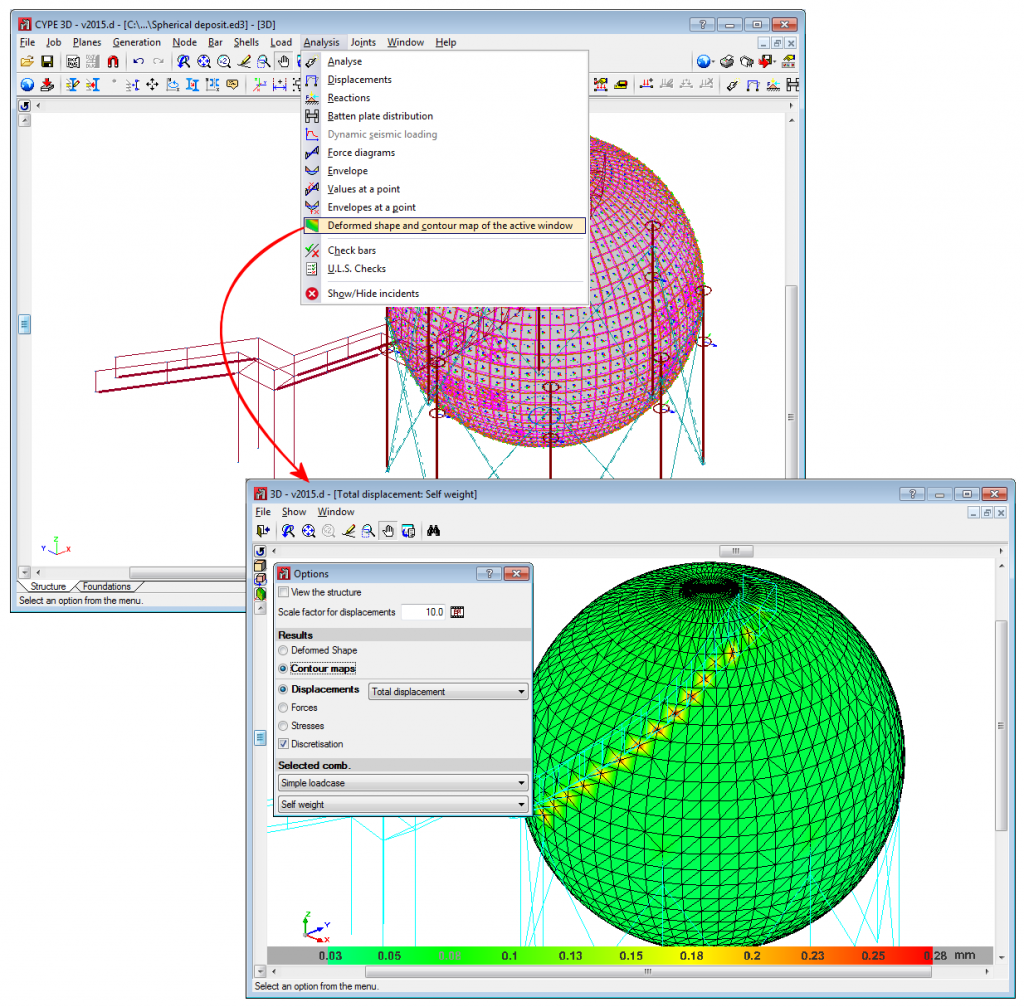
Earthquake-resistant systems according to ANSI/AISC 341-10, and prequalified connections according to ANSI/AISC 358-10 and ANSI/AISC 341-10
CYPE 3D allows the main specifications and requirements linked to the three most common seismic-resistant systems defined in the American standard AISC 341-10 (Seismic Provisions for Structural Steel Buildings) to be included in the design of rolled and reinforced steel structural elements: moment-resistant frames, frames with concentric bracing and frames with eccentric bracing.
CYPE 3D also analyses, designs and checks Prequalified Connections according to ANSI/AISC 358-10 (Prequalified Connections for Special and Intermediate Steel Moment Frames for Seismic Applications) and ANSI/AISC 341-10.
For more information on these CYPE 3D features, please visit the earthquake-resistant systems and prequalified connections page.
Fire resistance check
Using the new Fire resistance check module, CYPECAD and CYPE 3D carry out the following:
- For steel columns, beams and bars
The required fire resistance checks and protection coating design in accordance with the CTE DB SI 6 code and Eurocodes (EN 1992-1-2:2004 and EN 1993-1-2:2005). - For timber beams and bars
The required fire resistance checks and timber section design in accordance with the selected code (CTE DB SE-M –Spain-, NBR 7190 or Eurocode 5).
More information about these checks can be found on the Fire resistance check webpage.
Welded and bolted joints
The Joints modules designed by CYPE (Joints I. Welded. Warehouses with rolled and welded steel I sections, Joints II. Bolted. Warehouses with rolled and welded steel I sections, Joints III. Welded. Building frames with rolled and welded steel I sections, Joints IV. Bolted. Building frames with rolled and welded steel I sections, and Joints V. Flat trusses with hollow structural sections) can be used in both CYPECAD and CYPE 3D (including the Integrated 3D structures of CYPECAD).
The type of joints resolved in the Joints I, Joints II and Joints V modules are more applicable to warehouses designed in CYPE 3D and in Integrated 3D structures of CYPECAD, whilst the joints designed by the Joints III and Joints IV modules have a wider field of application in building structures formed by frames that are designed in CYPECAD. Nonetheless, each joint designed by any of the indicated modules is resolved in the same manner regardless of the program used. Furthermore, the Joints I, Joints II, Joints III and Joints IV modules contain several types of joints common to both modules.
More information on the properties of these modules can be found at the following links:
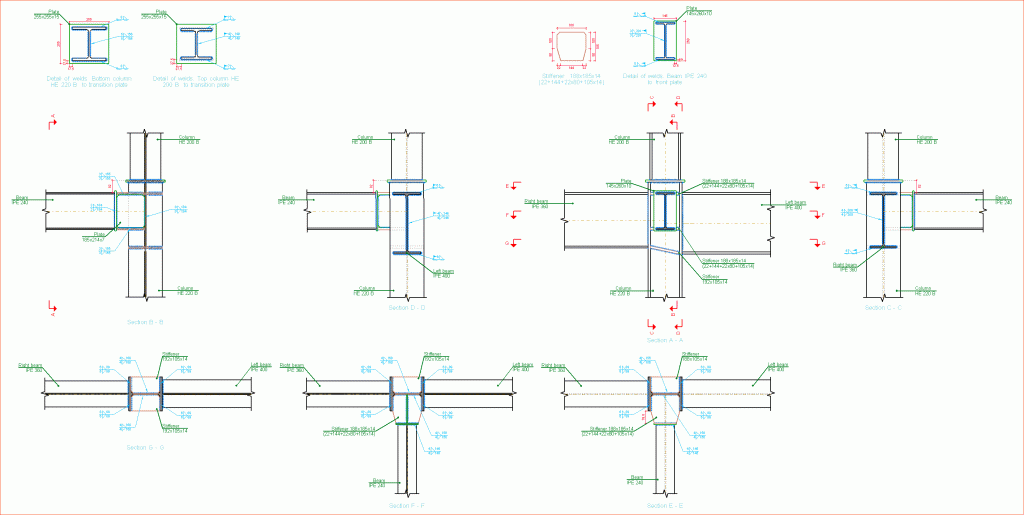
- Implemented codes for the design of building bolted connections
- Implemented types of building bolted connections
- Design options
- Prestressed and non-prestressed bolted connections
- Bolted connection design
- Design criteria for prestressed bolted connections
- Joint consultation
- Baseplates designed using the Joints IV module
- Joints report
- Bolted joints drawings
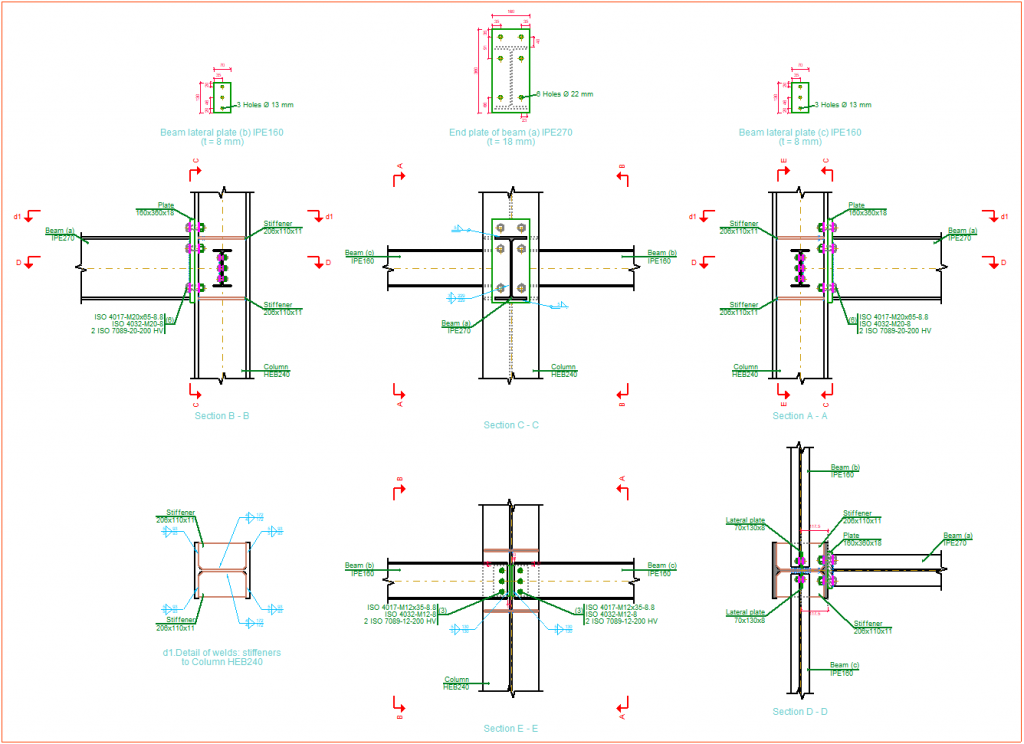
Baseplates
CYPE 3D has several modules that allow baseplates to be edited, checked and designed: the Baseplates module and the Joints I, Joints II, Joints III and Joints IV modules. The “Baseplates” module resolves baseplates for any steel column layout and the joints modules only resolve welded baseplates of rolled and welded steel I sections.
The properties of the designed baseplates are described below.
Properties of the baseplates included in CYPE 3D
- Baseplate types
- Baseplates module
Designs, edits and checks welded baseplates for any steel column layout (simple and built-up sections, rolled, reinforced and cold-formed sections). It does not include the analysis and design of welds between plates, stiffeners, columns and bolts except for rolled or welded steel I sections. - Joints I, Joints II, Joints III, Joints IV modules
Designs, edits and checks welded baseplates in rolled or welded steel I sections.
- Baseplates module
- Welds: Includes the analysis and design of welds between plates, stiffeners, columns and bolts.
- Editing baseplates: Users can edit baseplates, modify them manually and check whether their requirements are met.
- Automatic matching: Automatically matches the baseplates in the same job (considering the type of section, forces and exterior fixity). This way, and without user intervention, the number of different plate types is reduced, obtaining more uniform results.
- 3D view with differentiated elements and welds: A 3D view with different colours for plates, columns, stiffeners, bolts, welds made in the workshop and welds made on-site can be displayed on the screen, as well as the connections between steel I sections. This helps improve the understanding of the support assembly.
- Baseplate detailing: A detailed view of the plate is generated showing the details of the designed welds and the details of the stiffeners. This detailed view can be included in the project drawings.
- Check and quantities reports: Check and quantities reports are generated for the resolved baseplates, integrated with the remaining analysed joints.
Baseplate design options
The baseplate design options are configured in the Options dialogue box (Joints menu > Options).
Baseplate checks
CYPE 3D carries out the following checks to design baseplates (assuming the rigid plate theory):
- The concrete supporting the plate is checked for the following:
- Compression stress: The compression stress on the baseplate-concrete interface must be less than the allowable stress of the concrete that depends on the nature of each combination.
- Anchor bolts are checked for the following:
- The material resistance of the bolts: The forces acting on the plate are separated into axial and shear forces in the bolts and it is verified that both forces, when acting separately and interacting between them (Von Mises stress) produce stresses lower than the limit stress of the bolt material.
- Anchorage of the bolts: The anchorage of the bolts in the concrete is checked so that it does not fail because of bolt stripping due to adherence problems, concrete cone or shear failure (crushing).
- Crushing: Each bolt is checked to verify that the shear that would cause the plate to crush against the bolt is not exceeded.
- Baseplates are checked for the following:
- Global stresses: In baseplates with overhang, four sections are analysed in the perimeter of the section, all of which are checked to ensure that the Von mises stresses are less than the limit stress in accordance with the standard.
- Relative global deflections: The overhanging sections of baseplates are checked to ensure that the deflections do not exceed 1/250 of the overhang.
- Local stresses: The Von Mises stresses are checked in all the local plates in which both the section and the stiffeners divide the baseplate itself. The forces in each of the subplates are obtained from the contact stresses with the concrete and the axial forces of the bolts. The generated model is solved by finite differences.
Foundations
CYPE 3D analyses and designs footings and pile caps. Both foundation elements can be isolated or combined, i.e. they may support any number of columns.
Footings can be made up of reinforced concrete or mass concrete, with constant or variable depth, and the program can design them to be square, rectangular, eccentric, corner or edge centred. The analysis and design of the footings is part of a CYPE 3D module.
Pile caps admit multiple piles. A wide range of types is available. They may hold 1, 2, 3 and 4 piles; linear pile caps and rectangular pile caps for any number of piles (from 3 to 30 per side); pentagonal pile caps for 5 and 6 piles, and hexagonal pile caps for 6 and 7 piles. The analysis and design of the pile caps is part of a CYPE 3D module.
Both footings and pile caps can be supported by tie straps and centring beams. The design of strap and tie beams is included in the footings and pile caps module.
More information on the foundations designed by CYPECAD and CYPE 3D can be found on the Advanced design of surface foundations webpage.
CYPE 3D allows the balancing type of the ends of centring beams to be chosen by selecting the bearing pressure distribution acting under the footing in response to the soil, in order to analyse the forces on the centring beam and the pressures of the soil.
- Rectangular pressure distribution under the footing:
If this option is selected, the balancing of the beam is perfect, resulting in a rectangular pressure distribution in the soil.
- Trapezoidal pressure distribution under the footing:
The balancing of the beam is not perfect, i.e. a certain amount of rotation of the footing occurs, resulting in trapezoidal pressure distribution and, therefore, a reduction of the forces acting on the beam. If there is a trapezoidal pressure distribution under the footing, its resultant is displaced towards the column, resulting in a reduction of the moment on the beam of approximately 10%.
Help with data introduction
Data introduction assistant
When a new job is created in CYPE 3D, an assistant is displayed that helps users introduce the general data of the job:
- Codes (Concrete for foundations, Rolled and welded steel, Cold-formed steel, Timber and Extruded aluminium) and activating the seismic code (dynamic spectral analysis).
- Additional loadcases.
- Limit states (load combinations).
- Steel data (rolled or welded and cold-formed).
- Timber data.
- Extruded aluminium data.
- Foundation data.
The data of the material introduced in the assistant is the default data that will be assigned to each introduced element. Using the Describe material option in the Bar menu, a material other than the default material can be assigned to any element for the job.
All the data introduced in the assistant can be modified once the assistant has closed. These changes can be carried out in the Project menu in the Structure tab and in the Project menu > General data of the Foundations tab. For this reason, the Extruded aluminium sections option has been added to the Project menu so the default data for this material can be modified.
IFC file import
CYPE 3D allows for structural analysis models to be imported by means of an IFC file. IFC files that only contain the physical model and not the structural analysis model, do not contain any information that can be read by CYPE 3D.
In IFC format files, the structural analysis model is composed of structural type entities, such as nodes, bars, loads, etc. The connections between nodes and bars are also defined explicitly by using fixity conditions. It is similar to the model that users define in CYPE 3D.
The entities that CYPE 3D imports from the IFC files are the following:
- Nodes (IFCStructuralPointConnection), with their external fixity conditions.
- Bars (IFCStructuralCurveMember), with their end fixity conditions and their descriptions.
Entering the bars of the structure
CYPE 3D imports files generated in CAD programs in DWG and DXF format in two and three dimensions. Using these files, the geometry of the structure can be generated automatically (even selecting the elements to be imported classified by layers, entities, colours or line types).
Drawing files in DXF or DWG format can also be imported to be used as drawing templates. This way, users can enter the nodes and bars of the structure by snapping the entities and elements of these files in the 2D windows of the program. The import and use of DXF and DWG files are carried out in the same way as in CYPECAD. Users have three buttons available in the toolbar to manage the use of these files:
Imports the DXF or DWG format files and allows for their layers to be managed.
Activates or deactivates the view of the imported DXF or DWG file in the active window.
Manages the settings for snapping entities and elements of the DXF or DWG files that are displayed in the 2D windows of the job.
Other tools are also available to facilitate data introduction: Zoom, Redraw, Orthogonal, Undo, Redo, Repeat last element selection, etc. Object snaps (end, midpoint, perpendicular, nearest and intersection) and tracking (extension, perpendicular, orthogonal) can be carried out on elements of the structure.
With the view generation, users can work with 2D and 3D windows (of the entire structure or just a part of it) in a completely interactive way and with total connectivity. Even in the 3D windows that appear on screen, the plane of the 2D window where the cursor is positioned is marked.
CYPE 3D also includes tools for automatically generating elements, such as nodes, bars and spatial meshes made up of tetrahedrons. It can also create an unlimited number of parallel frames based on a single frame.
Elements are dimensioned without entering coordinates or rigid meshes. When a node or bar is entered, the program assigns them a set of coordinates that depend on the position of the cursor on the reference line or lines that are snapped. Then, users can dimension the nodes or leave the assigned coordinates.
Analysis using multiprocessors
CYPECAD and CYPE 3D use the potential of multiprocessors in the analysis of their structures.
To access these features, CYPECAD and CYPE 3D have two new common modules that save a substantial amount of analysis time:
- Parallel analysis with two processors
- Parallel analysis with up to eight processors
More information on these modules and a comparative study displaying the analysis duration with and without their use can be found on the Analysis with Multiprocessors webpage.
Results, drawings and reports
The force and deformed shape diagrams and envelopes can be consulted graphically or analytically on screen.
The tool for checking bars on screen, (stress, denting, slenderness, deflection, etc.) allows a manual or automatic correction to be carried up to the final design.
It generates the drawings of any view of the structure, with all the required information, including elevations with real section dimensions. The drawings can be exported in DXF and DWG format or printed using a printer or plotter.
It generates 3D views with perspective or isometric projection displaying the sections with their real size. The 3D views can be printed and exported in DXF, DWG, EMF, BMP and JPG formats. In these views, elements can be displayed with textures resembling the real colours of their materials. Users can represent the 3D view with or without the materials:
- Without materials
Displays the colours that differentiate the elements of the 3D view even if they are the same material. - With materials
Displays the elements of the 3D view with textures resembling their real colours.
Free movement within the structure is permitted with perspective projection.
Provides data reports for nodes, bars and loads: reports of displacements, reactions, forces, stresses, deflections, footings, baseplates, etc. in the structure. It includes quantities reports. These reports can be exported in TXT, HTML, PDF and RTF formats. A preliminary view of these reports can also be obtained.
Detailed ultimate limit state check reports
CYPECAD, CYPE 3D and the Integrated 3D structures of CYPECAD generate detailed reports on the ultimate limit state checks of steel and aluminium sections.
These reports contain all the checks carried out by the program for designing sections and constitute an important document with which the user can:
- Verify the design of the sections.
- Optimise the design of the sections.
The level of detail of these reports also acts as a detailed guide that allows users to familiarise themselves with all the checks to which a section is submitted.
More information about these documents (how they can be obtained, section types and codes for which they can be generated) can be found at Detailed ultimate limit state check reports.
CYPE 3D versions
CYPE 3D (without modules)
The basic version of CYPE 3D (without modules) analyses three-dimensional structures of nodes and bars with steel sections, concrete and generic materials, and flat shells. It supports tension-only tie rods and obtains the design and checks of steel section bars. The features of this basic version of CYPE 3D can be increased by adding any of the CYPE 3D modules to the user license.
CYPE 2D
CYPE 3D version limited to two-dimensional analyses. This version optionally offers the same modules as CYPE 3D.
Other features
CYPE 3D modules
In order to access further features offered by the program, there are several modules that can be found on the “CYPE 3D modules” webpage.
Interoperability with other systems
CYPECAD, 3D structures integrated into CYPECAD, and CYPE 3D can export the analysed and designed structure to TEKLA Structures. More information on export options can be found at How to export from CYPE to TEKLA® Structures?